Order Processing at Omara: A Step-by-Step Journey
Ever wondered what happens after you place an order at Omara?
In this guide, we’ll take you behind the scenes and walk you through each step of our order processing journey — from checkout to delivery. .
At Omara, each order is carefully crafted through a meticulous manufacturing process to ensure that customers receive only the highest-quality products. While some in-stock items can be shipped immediately, most orders at Omara undergo a comprehensive production process. Here is an overview of the typical order journey, along with the lead times and the key stages involved:
1. Order Receipt
The journey begins once the order is received. This marks the first step in ensuring that every detail is captured correctly before the manufacturing process begins. Omara’s dedicated customer service team ensures that all order specifics are addressed.
2. Customer Service Validation
Customer service validates the order by addressing any specific requests made by the customer, such as engravings or special stone requirements. This step ensures that the product will meet all personalized needs. If applicable, customers can choose unique engravings or even request specific types of stones for their jewelry.
3. Manufacturing Placement
Once validated, the order is placed into the manufacturing queue. This is where the actual creation of the product begins.
4. Design Modifications
For products that require modifications or customizations, the next steps include:
- CAD Design: The first phase of the design modification is creating a detailed 3D design of the product. The CAD (Computer-Aided Design) allows for precision and accuracy in the design before any physical manufacturing begins.
- Mold Creation: Following the CAD design, a mold is created to shape the product precisely according to the design specifications.
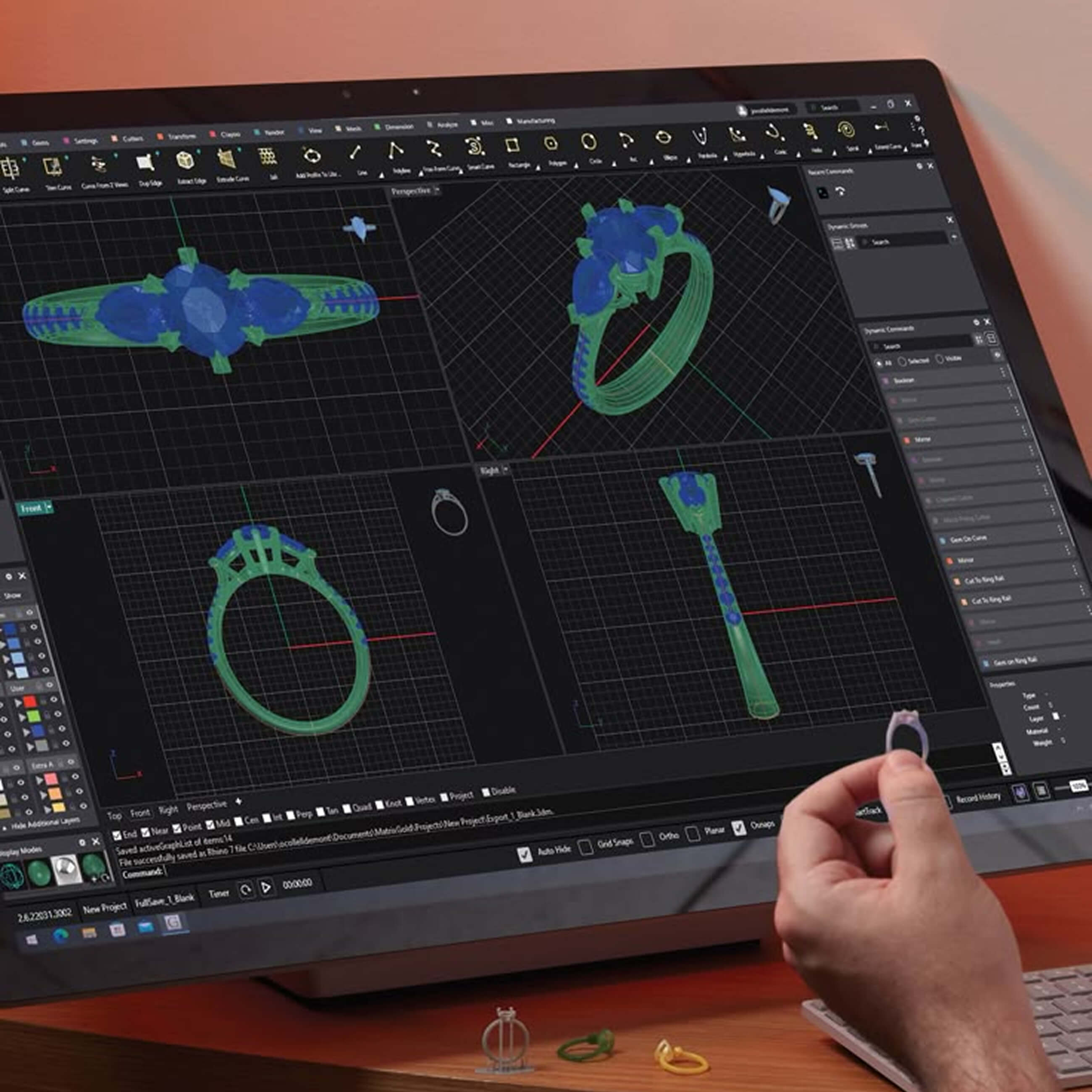
5. Metal Component Manufacturing
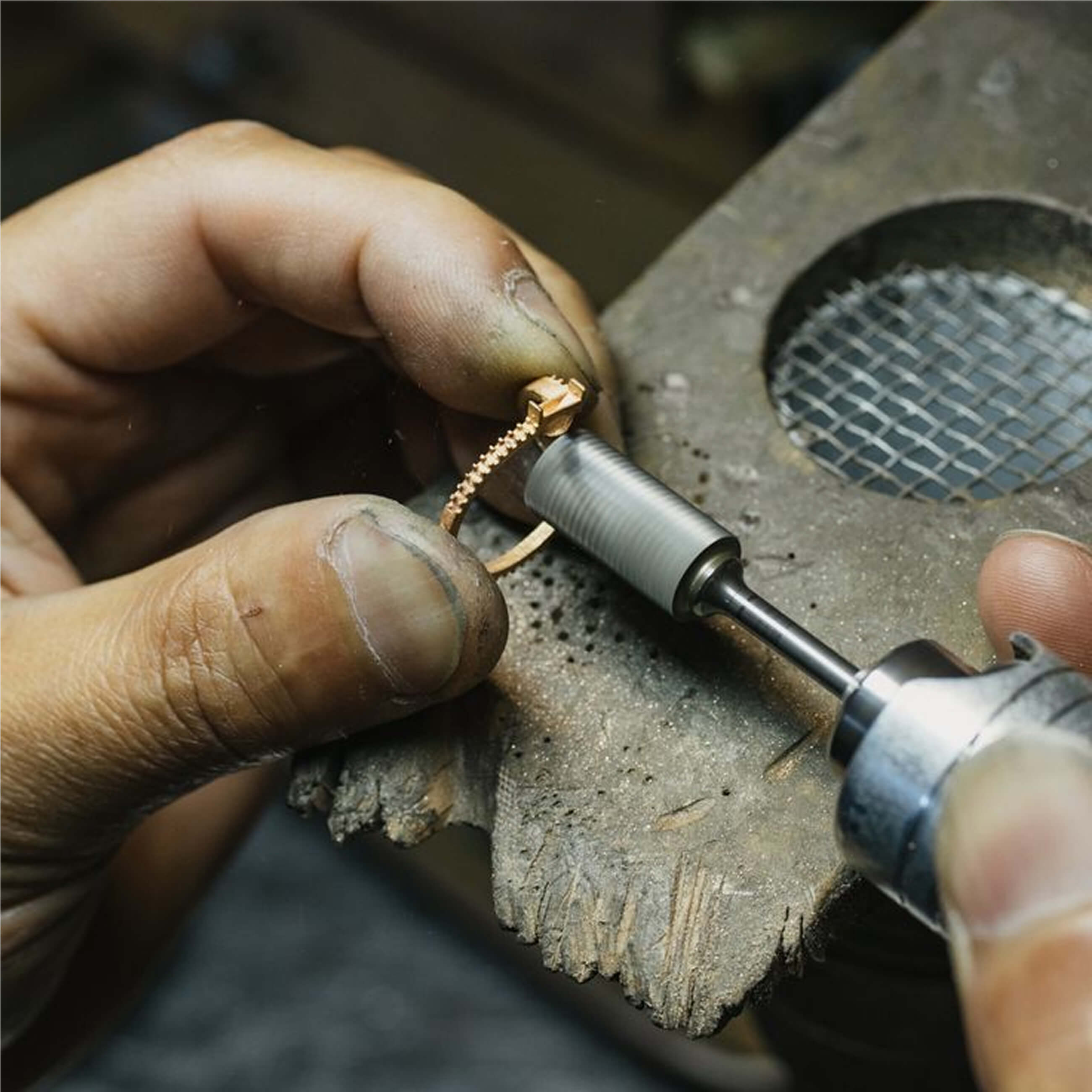
Once the design and mold are approved, the metal components of the product are manufactured. This involves casting and shaping the metal according to the specifications laid out in the CAD design.
- Metal Preparation
- Casting
- Cooling & Solidification
- Mold Removal & Initial Cleaning
- Shaping & Assembly
- Polishing & Surface Treatment
- Preparation for Stone Setting
6. Stone Setting
After the metal components are ready, the next step is to carefully set the stones into the jewelry. Whether it's diamonds, sapphires, or any other precious stones, this process requires precision and craftsmanship.
- Marking and Drilling - precise measurements are taken to mark the exact spots for stones.
- Creating Seats - tiny seats or grooves are cut to perfectly fit each stone.
- Setting the Stone - the stone is gently placed.
- Securing - locks the stone in place, ensuring stability without damaging the gem.
- Polishing Around the Setting - to blend seamlessly with the rest of the design.
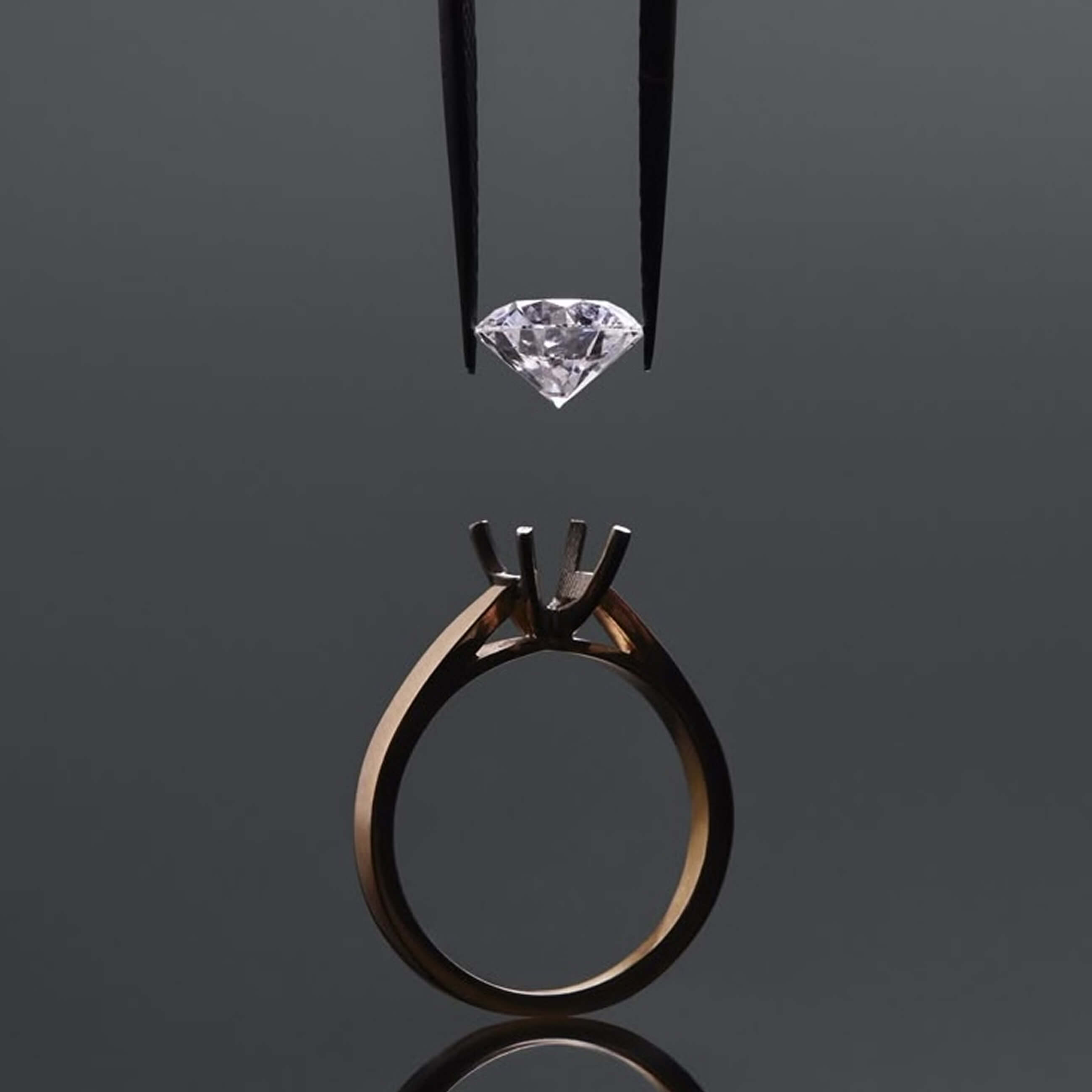
7. Significant Stone Verification
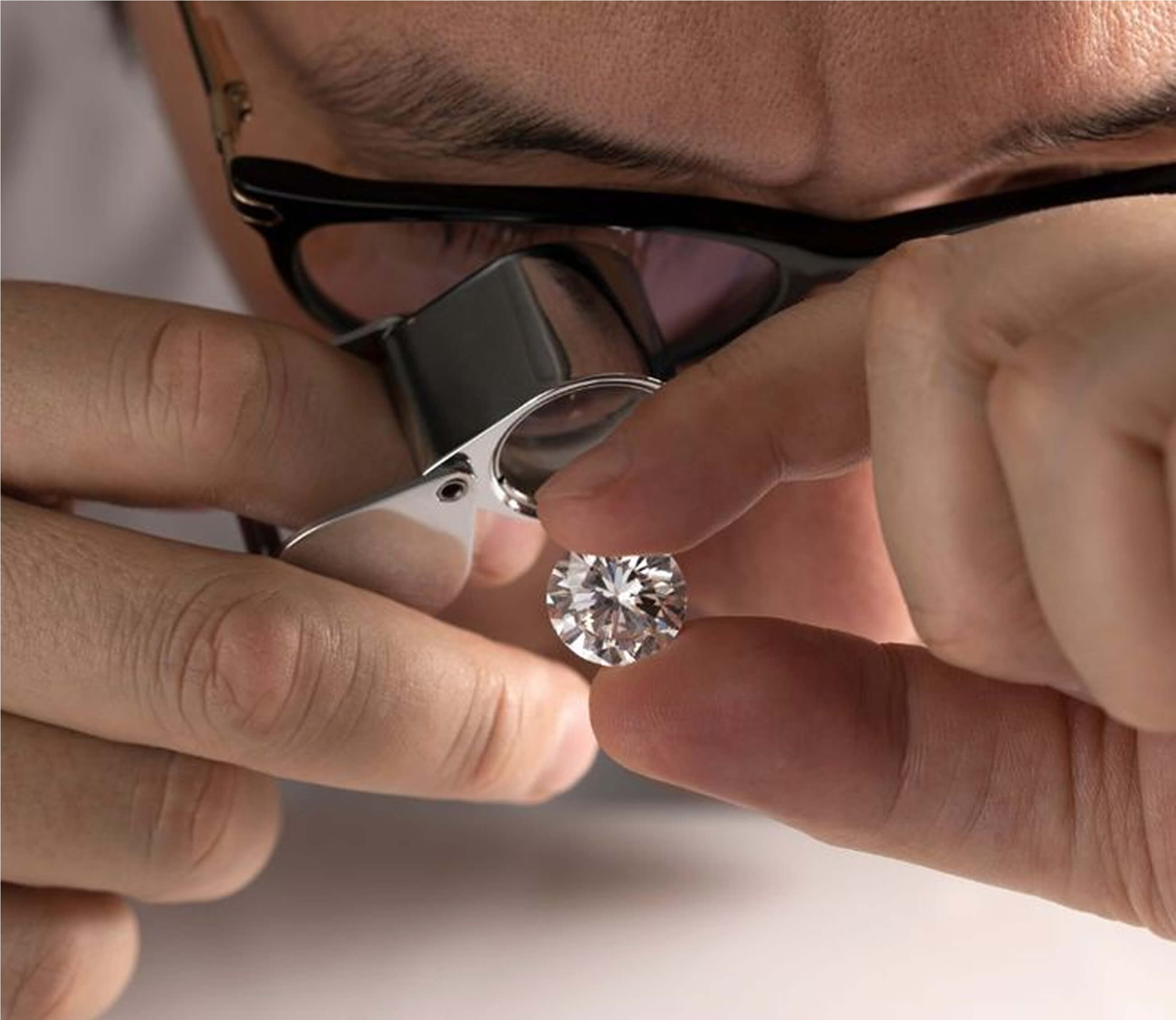
For products that feature precious stones, the stones are carefully matched to their corresponding certificates. This verification process ensures that the stones meet the required specifications, guaranteeing their authenticity and value.
Every significant stone — such as diamonds, sapphires, emeralds, or other rare gemstones — comes with its own certificate issued by a recognized gemological authorities - GIA / IGI. More about gemstone certificates you can read here
8. Personalization
If the customer has requested additional personalization, such as engraving on a ring or bracelet, this is done at this stage. Engravings are carefully executed to ensure they are legible and precisely placed.
If the customer has requested an engraving — whether it’s initials, a date, a name, or a personal message — this is completed with extreme precision after the stone setting and polishing phases.
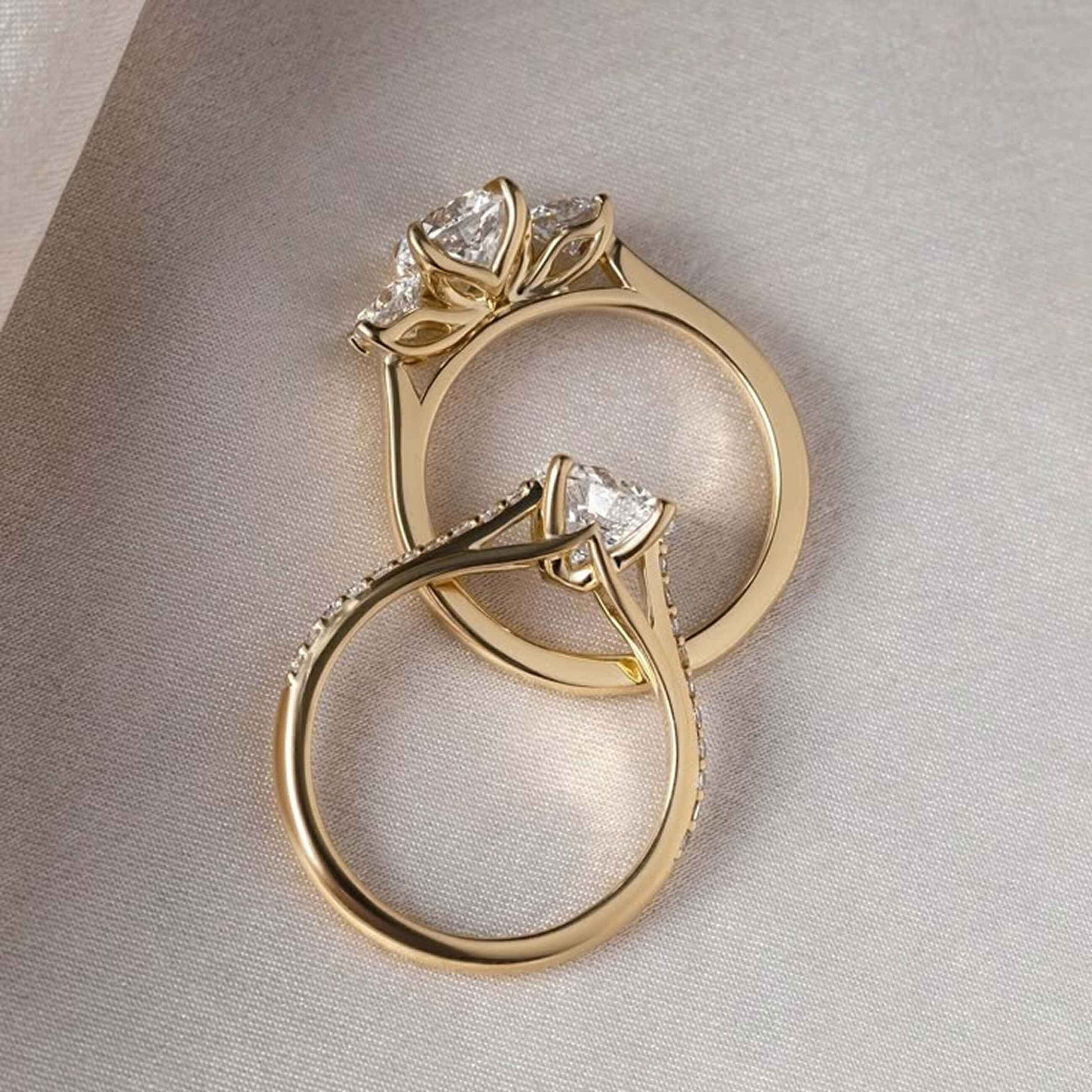
9. Quality Control (QC) at the Factory
Once the product is completed, it undergoes a thorough quality control (QC) process at the factory. Skilled inspectors check every detail to ensure the product is flawless and meets Omara’s high standards.
After passing the initial QC checks, the factory submits a report and photos of the product to Omara’s QC team. This submission includes verifying the hallmark and stone authenticity, ensuring everything matches the original specifications and customer requests.
10. Delivery to Omara's EU Fulfillment Center & Customs Processing
Once the product is approved, it is shipped to Omara's EU fulfillment center for further processing.
If applicable, the product undergoes customs processing to ensure it meets international shipping regulations. This step is crucial for international orders. More information about our delivery process you can read here
11. QC by the Fulfillment Team
Upon arrival at the fulfillment center, Omara’s fulfillment team performs another round of quality checks to ensure the product is still in perfect condition and matches all specifications.
12. Shipment to the Customer
Once all QC procedures are complete and the product is deemed perfect, it is finally shipped to the customer. Depending on the location, the product will be delivered via a reliable shipping service to ensure timely delivery.
Throughout the entire process, Omara focuses on precision, personalization, and quality, ensuring that every customer receives a product that exceeds expectations. Whether it’s a custom design, a special engraving, or the careful selection of gemstones, Omara’s order processing system guarantees attention to detail at every step.